Embracing the Aging Workforce with Modern Loading Dock Solutions
America’s workforce is aging. Currently, the average age of highly skilled manufacturing employees is 56, and nearly one-third of all manufacturing professionals are over 50. With ongoing labor shortages and younger generations choosing other occupations, this disproportionately small demographic of “baby boomers” comprises majority of warehousing and distribution jobs.
Unfortunately, while robotics, automated shipping and receiving (AS/RS) systems, AGVs, and 3PL warehouse management systems have taken industrial facilities into the 21st century, many loading dock operations still use manual labor and 20th century technologies and practices. For aging workers, these practices can be back-breaking, literally. But luckily, that is changing.
From automatic vehicle restraints to push-button hydraulic levelers with Smooth Transition Dok System® features and integrated loading dock control systems, solutions from Rite-Hite help ease manual labor at the loading dock by providing relief to the backbreaking work of the past. In addition to the ergonomic benefits for workers, interlocked, integrated loading dock control systems are another example of how loading dock modernization is making the loading dock safer and more efficient for all employees.
Automatic Vehicle Restraints
In the not so distant past, dock levelers, overhead doors, and vehicle restraints were operated (placed) manually. These types of manual operations are not only time intensive but can be life threatening to the host of potential accidents caused by human error. For example, manually placing wheel chocks oftentimes places dock workers outside on the dangerous drive approach without proactive communication and threat detection. With OSHA reporting tractor-trailers as the second leading cause of back-over deaths in the country, paired with the aging workforce and labor shortages, it is critical for facilities to reduce the amount of process that place “boots on the ground” outside on the drive approach with large trucks and semi-trailer maneuvering about. One of the most immediate solutions for helping keep valued workers safe at the loading dock is an automatic vehicle restraint.
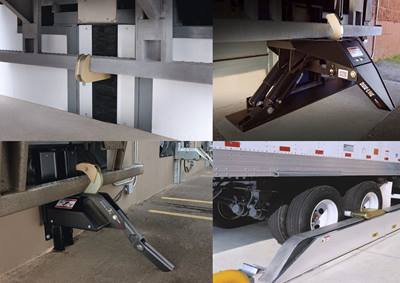
Over the last 40 years, vehicle restraints have been developed for all applications to automatically secure a trailer to the loading dock with the push of a button. This level of automation helps docks operate safer and more efficiently, in addition to helping keep boots off the ground outside on the drive approach. Automatic vehicle restraints also address traditional trailer separation accidents, such as a driver prematurely pulling away (early departure) from a dock when a forklift is still inside, helping to mitigate the risk of a forklift running off the 4 foot drop off which can result in severe or even fatal injury to the driver.
All Rite-Hite vehicle restraints are equipped with constant light communication as well as the ability to incorporate additional Rite-Vu™ Hazard Recognition and Control safety features to support the aging workforce. They are also all compatible to be integrated with Rite-Hite hydraulic dock levelers.
Push-Button Levelers
Once a trailer is properly secured by a vehicle restraint, loading dock operators must bridge the gap from facility floor to the back of the trailer with a dock leveler. Mechanical levelers can require up to 70lbs of force to pull a chain and raise the leveler. Then the weight of the dock attendant’s body to walk down the leveler, or worse, unsafe jumping methods to lower, if weight isn’t enough. This might be sufficient for smaller operations with few dock positions that do not have a high volume of trailers to service, and a younger workforce. However, for aging workers and high-volume operations, it’s important to seriously consider the ergonomic alternative of hydraulic levelers.
By using a hydraulic dock leveler with push-button controls, workers go from continuously bending over and pulling a chain, to the simple push of a button to raise and place the leveler. Considering the typical loading dock leveler services on average eight trucks per day, this repetitive removing action helps prevent acute / chronic injuries with less trips to the chiropractor . A bonus feature of constant contact leveler controls is the added layer of pedestrian pit safety because it keeps the operator safely behind the control box during all leveler operation.
Pit Safety is especially important in Drive-Thru applications, which also help to reduce processes that place workers on the dangerous drive approach by allowing facilities to open trailers on the inside. This is accomplished with a vertical storing leveler, that when in the stored position, exposes a pit that's ideal for ease of maintenance and cleaning - but also the potential for human error
Smooth Transition Dok System
Forklift operators cross the threshold from facility floor to trailer bed more than 100,000 times each year. For each back and forth crossing over the dock leveler, there are 8 main transition points that are common areas where forklift drivers feel more of the “speed bumps” – rear hinge, leveler platform, front hinge, leveler lip and over each again back into the facility. Rite-Hite developed a Smooth Transition Dok System to help combat WBV at each of these points.
Rear Hinge: As the leveler raises and lowers, this hinge can create gaps that become trip or shear points for forklifts and pedestrians. A
constant radius rear hinge limits this gap to a 1/3”, no matter the leveler position - helping reduce WBV, protect pedestrians crossing, and prevent debris from falling into the leveler pit.
Front Hinge: This transition point of a dock leveler is one of the highest moving components and withstands a considerable amount of the cargo’s weight. A leveler with
two-point crown control allows the hinge to be supported in to points of contact (back edge of the lip and underside of the lip), while its uniquely shaped front header helps to control the crown; providing only what the facility needs . This helps to extend the life of the lip hinge, while reducing the “speed bumps” felt during the loading process
Leveler Platform: Levelers use beams to support the platform, each with a varying degree of strength and rigidness. This is important when it comes to servicing a trailer with an uneven load. A leveler with a
self-flexing deck allows the platform to flex under it’s own weight vs. the weight of the forklift. Levelers that require weight to meet the trailer floor may raise up when weight is removed – creating a hazardous gap that can cause serious harm to forklift driver, equipment, and products.
Leveler Lip: The last crossing point can cause significant impact to the forklift driving depending on the angle into the trailer. A leveler lip with an optimized or extended lip chamfer can help make the transition more gradual and limit WBV.
Bonus: When paired with a Stabilizing Trailer Restraint relative smoothness from leveler to trailer is improved upward of 120%.
Whole Body Vibrations (WBVs)
To better understand the bodily effects on forklift drivers, a study was conducted by The Ohio State University. It revealed that selecting a dock leveler designed with a Smooth Transition Dok System® directly reduces the effect of Whole Body Vibration (WBV) by up to 16% - over 50% when paired with modern forklift designs. Considering one in two Americans experiences back, neck and should pain, which translates to over 252 million adults who are in pain, significantly reducing WBV spares the aging workforce from the key contributors to long-term chronic back, neck, and even leg injuries.
Loading Dock Controls
Traditionally, loading dock walls were cluttered with individual control boxes for each piece of equipment- including vehicle restraints, levelers, overhead doors. This can be confusing, leading to more room for human error, and often increases the time taken to train new employees - it too can now be a thing of the past. The most advanced dock controls now seamlessly integrate compatible equipment systems into one, interlocking, control panel.
It starts with the vehicle restraint. Once it is properly engaged with a RIG or rear wheels to help secure the trailer, the vehicle restraint enables dock workers to use other equipment in a customizable safe sequence of operations that fits their equipment and application. For instance, these systems can be programmed with a green light interlock, which disables the use of the hydraulic leveler and/or overhead door until the vehicle restraint is safely engaged (green light on the inside of the loading dock); an overhead door interlock, which requires overhead doors to be opened prior to leveler operation; or a stored leveler interlock, which ensures that the leveler is stored safely before the restraint can release the trailer. This type of control panel helps to eliminate the potential for human errors when it comes to operating equipment at the loading dock door.
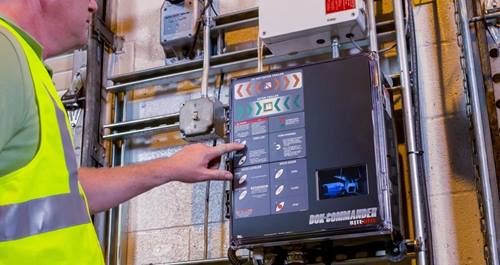
Advanced control systems use a modern NEMA 4X rated user interface with membrane switch buttons and are built to withstand the harsh conditions of a loading dock to meet requirements for electrical noise, and harsh environmental conditions. In addition, they have flexible circuitry and can be modified to update components or add features as needs change or budgets allow.
Automating Safety
Working on a loading dock doesn’t have to be a major pain for anyone young or old. Facility managers are more aware than ever about the environment their employees are working in, many of whom have recently committed to agreements such as the MSD Pledge, which promises to reduce workplace musculoskeletal disorders (MSD) injuries by 25% by 2025. Facilities and top leaders recognize the need to improve their equipment with more automated solutions for not only the aging workforce, but for all employees, because more advanced equipment can also simultaneously improve efficiency and safety.
Automatic vehicle restraints, hydraulic levelers with Smooth Transition Dok Systems and interlocked loading dock control systems are just three ways facilities can provide ergonomic safety solutions for workers. If your facility is still simply chocking tires, manually operating mechanical levelers or using levelers designed without smooth transition technology, it is time for an upgrade.
Contact a Rep to Learn More