- Home
- News
- The Benefits of Hydraulic Conversion for Mechanical and Air Levelers
The Benefits of Hydraulic Conversion for Mechanical and Air Levelers
According to the National Association of Manufacturers, nearly 25% of the manufacturing workforce are 55 years or older. Defined as the "aging workforce", these employees are more susceptible to acute and chronic injuries. When operating heavy machinery, forklifts, or loading dock equipment such as levelers, the need for a solution that provides improved ergonomics and a smooth transition from trailer to warehouse floor becomes a top priority.
When considering these priorities, equipment such as mechanical levelers, which require employees to bend over to pull a chain or manually walk the leveler down onto the trailer bed, can cause unneeded stress on an employee's body. These situations can be especially detrimental for the aging workforce and can make working in a manufacturing plant difficult and uncomfortable. It's important for facilities to ensure their equipment not only efficiently moves product, but also keeps their employees healthy and safe. One immediate, cost-effective consideration a facility can make is converting existing air and mechanical levelers into hydraulic operations with a hydraulic conversion kit.
What is a Hydraulic Conversion?
A hydraulic conversion kit replaces competitive or Rite-Hite mechanical or air powered levelers with a hydraulic system and simple push-button control for more ergonomic operation and fewer moving parts to help improve productivity, safety and employee comfort.
The Benefits of Hydraulic Conversion
There are multiple benefits to converting to a hydraulic leveler, including:
- Improved ergonomics by helping to reduce acute and chronic employee injuries
- Fewer moving parts with less maintenance needs and equipment downtime
- Increased safety and productivity at each dock position
When a dock leveler is out of service due to broken, worn, missing or unreliable components, a facility is losing productivity as that dock position cannot be used. Further, an operator constantly bending over to pull chains or walk a heavy leveler down can lead to potential chronic back injuries. In some instances, a poorly adjusted or maintained mechanical leveler can require more than one operator, resulting in unsafe conditions and wasted resources.
Ergonomic Relief
Mechanical levelers can require 55-70 lbs. of force to pull the chain and raise the leveler. The hydraulic conversion kit helps to provide ergonomic relief by eliminating strenuous chain pulling and the need to manually walk the leveler down. With a push button control box, it only requires one operator to simply push a button to raise or lower the leveler into position. A hydraulic power unit (the heart of the hydraulic leveler) houses and controls all the power needed to raise the leveler and extend the lip. By upgrading mechanical parts to hydraulic system components, there are fewer moving parts needed to operate the leveler, resulting in less replacements, repairs or adjustments which helps save money on maintenance costs, as well as improving productivity with less equipment downtime..
Free-Fall and Stump-Out Protection
On a mechanical or air leveler, mechanical safety legs are used for end-loading and help prevent rapid free-fall in the event of early trailer departure. As a trailer is unloaded, these safety legs can engage, causing stump-out, which can potentially result in neck and back injuries for material handlers driving over mechanical or air levelers. When converted to a hydraulic dock leveler, the velocity safety fuse (which is part of the hydraulic conversion kit), eliminates the need to use mechanical safety legs and helps protect personnel from injury and equipment from damage, in turn reducing maintenance needs.
Fewer Moving Parts
Mechanical
A mechanical leveler lip is activated by many moving parts (snubbing cable, lip latch, cam, etc.). By converting to a hydraulic leveler, the lip is raised by a hydraulic lip cylinder, reducing the number of parts needed and providing a smooth, controlled lip extension.
By converting to a hydraulic leveler, all the components that make up a hold-down ramp control system are replaced by the main hydraulic cylinder, which eliminates the risk of hold-down failure, helping to protect personnel and equipment.
Air
Air powered levelers utilize an air bag lifting mechanism, mechanical safety legs and a mechanical lip which consists of multiple moving parts. Air bags can act as a trap for debris which is time consuming to clean. Hydraulic components are less intrusive in blocking required cleaning procedures, helping to keep an overall cleaner leveler pit and improve productivity with reduced cleaning and maintenance time.
Increased Safety
All hydraulic conversion kits come standard with two additional safety features. First, the Safe-T-Strut™ to help support the leveler while employees are in the pit for enhanced maintenance safety. Second, 3/16" heavy-duty full range toe guards add a layer of pedestrian safety by helping protect fingers or toes.
Additionally, converted hydraulic operations facilitate interlocking capabilities which provide safer sequence of operations throughout the loading/unloading process. For example, loading dock leveler interlocks can be integrated with vehicle restraints and Rite-Vu components for improved safety and productivity throughout the sequence.
Rite-Hite’s Solution
With Rite-Hite hydraulic conversion kits, you can update both Rite-Hite and competitive dock levelers. By upgrading to hydraulic operation, you are choosing an easier, more ergonomic operation with fewer moving parts. Most importantly, your facility is investing in enhanced safety and productivity for their workforce and equipment. To help determine if it's time to upgrade or replace your existing Rite-Hite or competitive equipment or replace, reach out to your local representative today.
Contact Your Local Rite-Hite Representative
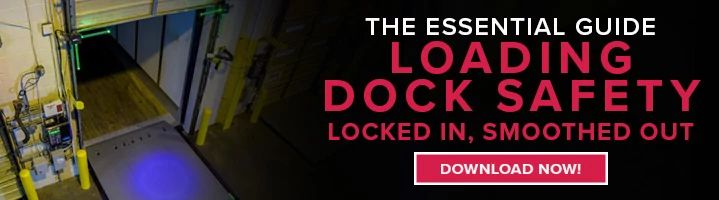