- Home
- News
- Designing the Right Loading Dock for Your Operation
Designing the Right Loading Dock for Your Operation
Although choosing the right loading dock equipment for your operations is critical to operational efficiencies, the foundation for safety and productivity is laid when designing the loading dock and yard. Understanding and planning for the unique requirements and needs of your facility will help mitigate future risk to your people, products and bottomline.
The main areas to focus during initial loading dock design which can directly impact a facility’s safety and productivity are:
- The drive approach outside of the building
- The loading dock height and openings
- Trailer to dock opening design
- The staging area inside the loading dock
Loading Dock Drive Approach
The loading dock is the main hub of a facility’s shipping and receiving with constant traffic throughout. So, it is critical that drivers have adequate space to back in and maneuver their vehicles - whether semi trailers or cargo vans. If the drive approach is too short or narrow, a facility is compromising both the driver’s safety as well as their throughput. And with today’s average tractor/trailer combined length reaching about 75 feet, a drive approach of only 110 feet, which was typical in years past, won’t suffice with today’s longer trailers.
Changes and trends in loading dock traffic and vehicle types impact loading design layout and equipment needs.
The American Trucking Association recommends that a drive approach should be twice the length of the longest tractor/trailer combination that a facility receives at their loading dock, plus an additional 5 to 15 feet depending on the overhead dock door centerlines. For example, a 75-foot tractor/trailer combo with 12-foot overhead door centerlines will need a drive approach of 165 feet (75 feet x 2 + 15 feet for the tight centerline).
Standard Loading Dock Height and Openings
The loading dock opening, which often needs to accommodate a dock door to separate inside from out, is another important measurement to be considered in loading dock design. However, the opening size should be based on types of trailers and traffic the facility plans to receive. Today, many trucks are operating on smaller rim and tire diameters, which is translating into the need for different loading dock heights. Common dock heights based on trailer type:
- Dry trailers: 46”
- City delivery trucks: 46-48”
- Refrigerated trailers: 48-50”
- Intermodal and overseas containers: 52”
While loading dock heights are getting shorter, loading dock openings are getting wider. Trailer widths are typically about 8-½ feet; however, dock openings should be a little larger to provide an easier target for truck drivers and better access for material handlers loading/unloading the trailer. In many cases, a 9 to 10-foot opening is the most ideal.
Trailer To Dock Setup Considerations
The height of the loading dock opening also affects the optimal leveler length. Loading Dock Levelers are needed in any facility to help bridge the gap from building floor to trailer bed. So the longer the leveler, the less slope for material handling workers to ergonomically maneuver in and out of the trailer.
Therefore, choosing the right leveler for your operations and ensuring it’s properly accounted for in the loading dock design is important.
On the most basic level, designers need to make sure the loading dock leveler fits within the frame of the loading dock door (typically about 9 feet wide) as well as the trailer (commonly about 8-½ feet wide). Loading dock levelers should be at least 7 feet wide to accommodate full-cube (packed trailer) loads, while still being able to fit within the frame of the trailer. The most common leveler length is 8 feet, which is important to note when accounting for the recessed pit area beneath the dock leveler.
Other considerations vary based on the application. For docks that deal with a large amount of intermodal and overseas containers, lowboy trailers, or have special dock heights, it is often advised to choose a longer leveler. In most cases a 10-foot or 12-foot long leveler will suffice. Longer levelers decrease the amount of slope, which improves safety for forklift operators, too.
Standard Loading Dock Slope
Drive approaches often have slope too, which should be taken into consideration for equipment application, water and weather drainage and more. Many new big box buildings are built with a level or slight incline of about ½-percent over the first 50 to 75 feet for drainage considerations. This small incline often isn’t a problem and the building can be protected from backing vehicles with modest bumpers near the bottom of the door.
However, declining approaches can lead to other problems. For example, the top of the trailer can come in contact with the building if the proper protection isn’t put into place. The easiest way to avoid this is to set the loading dock wall back 1 inch for every 1% decline. An additional 1 inch of bumper will also help with building and equipment protection at the base of the wall.
Size of Loading Dock Staging Area
The staging area, just inside the loading dock, is another area that should be carefully designed based on the trailers that are visiting regularly and the product being transported. If the trailer is a standard 53- to 57-foot over-the-road variety and carries full loads, it stands to reason the staging area needs a minimum of 53 to 57 feet to drop products. Most big box distribution centers build staging areas that are at least 75 feet deep to allow for forklift traffic and loading and unloading product. This is a trend in automation as well with some facilities choosing to install automated truck loading systems that can load a trailer with stagged pallets in one trip.
An important consideration in defining the staging area is where it begins in relation to the loading dock wall. Because most facilities won’t stack pallets of product immediately next to loading dock doors due to safety concerns and potential for blocking controls displaying restraint status, measuring the staging area from the end of the loading dock leveler is a recommended best practice. Some facilities like to have clear aisles set back at least 10 feet from the end of the leveler, which is why many big box stores have staging areas that often surpass an additional 20 feet inside the loading dock.
Building the Right Loading Dock Layout and Design
Taking the proper time to understand the factors that should be considered when planning for loading dock design layout will help save time and money for years to come. The ultimate payoff will not only be safer operations but reduced downtime, increased throughput and satisfied partners.
It’s never too early, whether designing a new building or reconfiguring and outfitting an existing facility, to engage with industry experts who can partner with architects, general contractors or anyone else who is charged with planning and designing industrial facilities with loading docks. Rite-Hite, as a leader in the material handling industry for over 55 years, understands all things from trends in traffic to requirements for building and loading dock equipment protection.
For assistance on properly designing loading docks, contact your local Rite-Hite Representative today. For additional resources, check out our Rite from the Source podcast episode: Loading Dock Design 101.
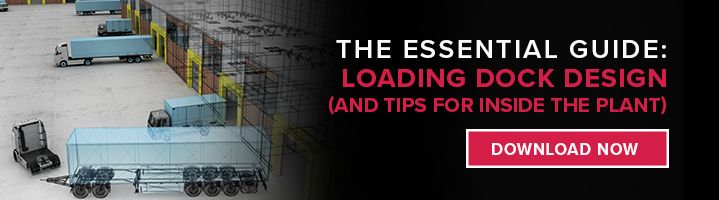
Contact Us