- Home
- News
- How To Contain Hazards and Protect Your Employees
How to Contain Hazards and Protect Your Employees
Today, successful industrial guarding requires understanding and applying codes and regulations, assessing risk, validating the safety system and its components, and applying prevailing machine guarding choices. Although many guarding methods and products are available, not all can be applied universally.
Understanding Codes and Regulations
OSHA codes are the rule book that MUST be followed. Understanding the “rules” set forth by OSHA and related specific referenced regulations will assure you that your company is providing a safe work environment. OSHA Title 29 CFR 1910.132 (d) (2) requires employers verify that a REQUIRED workplace hazard assessment has been performed through written certification that identifies the work place has been evaluated. To build on the Risk Assessment requirements the OSHA General Duties Clause states each employer shall furnish employees a place of employment that is free from recognized hazards that are or could cause death or serious physical harm.
Currently, the general requirements for all machines per OSHA 29 CFR 1910.212 (a) (3) (ii) states that the point of operation of machines whose operation exposes an employee to injury SHALL BE GUARDED. The code goes on to state that “in the absence of applicable specific standards: the machine “shall be so designed and constructed to prevent the operator from having any part of [his] body in the danger zone during the operating cycle.”
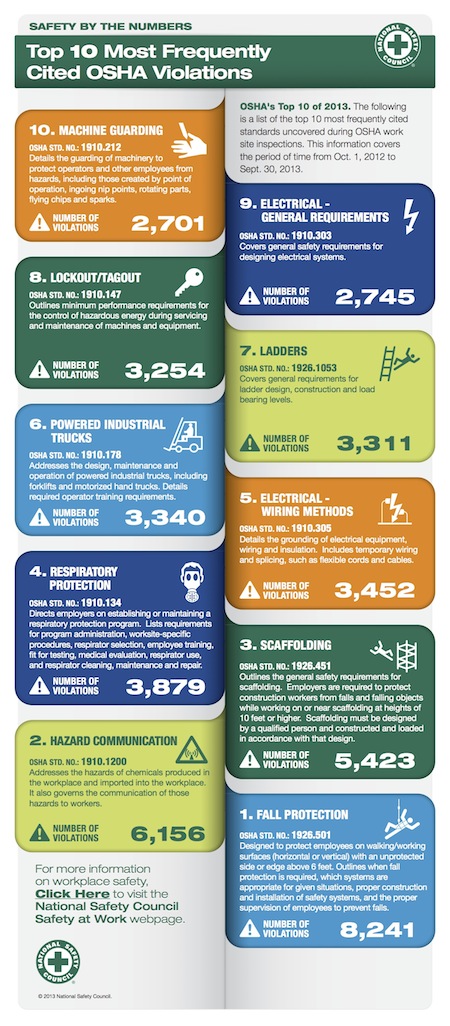
Assessing Risk
Facility managers looking to stay on top of the newest regulations can start by conducting a thorough risk assessment. Performing risk Assessments is NOT a one man job. To conduct a proper risk assessment many factors need to be considered which includes categorizing the level of risk, frequency of exposure , severity of the potential hazard among many other considerations. This requires input from machine operators, safety professionals, production managers, industrial engineers, plant mangers …. I think you get the idea, it takes a team.
When applying safe guarding devices, consider the following questions to get you started:
- Do the safeguards provided meet the minimum OSHA requirements?
- Do the safeguards permit safe, comfortable, and relatively easy operation of the machine?
- Is there a point-of-operation safeguard provided for the machine?
Validate the Safety System
Once the risk assessment is completed and a safety device is applied, it is required that you validate the system making sure the device is providing the proper level of safety according to applicable codes and regulations and achieving the desired result. Rite-Hite Machine Guarding solutions are designed to provide both an electronic means of monitoring safety (PLe, Cat 4 per EN ISO 13849-1, SIL 3 per EN 62061) as well as a high speed, high cycle automated physical means. By coupling these two aspects, Rite-Hite Machine Guarding products are capable of producing a higher degree of safety, helping contain manufacturing process and isolate any associated hazards.
Rite-Hite Machine Guarding Choices
GUARDS & PROTECTS – Guards your machinery and protects your employees
CONTAINS – Contains application driven hazards including airborne debris, heat, fumes, smoke, sparks, accidental discharge, spray/mist/fluids and mechanical movement
REDUCES FOOTPRINT – Reduces footprint of manufacturing cell by locating closer to hazard
Verti-Guard – Ideal for robotic cells, part assembly, and conveyor openings
Guardian Defender – Perfect for employee interaction with a machine, robot, or process
Slide-Air – Contain application driven hazards like weld sparks, mist, and debris
FlashFold – Unique vertical rising automated barrier door
Back to News