- Home
- News
- How to Specify the Right Loading Dock Products
How to Specify the Right Loading Dock Products
Between loading dock levelers, vehicle restraints, overhead doors, and loading dock enclosures, there are a series of choices to be made in order to create the safest and most efficient setup possible at your loading dock. If these choices are made carefully, safety and productivity can be built into these loading docks long before a forklift ever rolls across a leveler and into the back of a trailer. These basic considerations can help architects and general contractors find the right equipment based on the industry and the needs of the facility.
Loading Dock Levelers
Levelers are the heavy, steel bridge that gets forklifts from inside a loading dock area into the trailer to bring product into a facility or to send it out to customers.
Dock Leveler Size
On the most basic level, it’s important to make sure the loading dock leveler fits within the frame of the loading dock door (typically about 9 feet wide), as well as the trailer (commonly about 8-½ feet wide). Loading dock levelers should be at least 7 feet wide to accommodate full-cube (packed trailer) loads, while still being able to fit within the frame of the trailer. The most common leveler length is 8 feet, which is important to note when accounting for the recessed pit area beneath the leveler. Other considerations vary based on the application. For docks that deal with a large amount of intermodal and overseas containers, low boy trailers, or have special dock heights, it might be better to use a longer leveler. In most cases a 10-foot or 12-foot long leveler will do. Longer levelers decrease the amount of slope, which improves safety for forklift operators, too.
Types of Levelers
There are three different types of levelers that should be considered – mechanical, air-powered, and hydraulic. The decision is typically based on budget. The least expensive option, mechanical levelers, are operated manually and don’t need many special design considerations beyond the pit area. Air-powered levelers, which raise and lower the leveler with an air bladder, use an enclosed motor that requires electrical power. Hydraulic levelers, the most expensive and typically best option, use push-button controls that need electrical power, as well. It is also important to note the use of vertical storing dock levelers. These levelers are used in cases where environmental control is essential for a facilities business as these levelers allow the overhead door to close directly onto the pit floor, reducing dust, debris and rodents from entering the facility.
Safety Considerations
Another consideration when choosing a loading dock leveler is the safety features that come with it. Some levelers have built-in safety features, such as a lip at the end of the leveler to help prevent forklifts from falling off the edge of an open dock. Advanced levelers can be programmed into a safe sequence of operations into a single control box that interlocks the leveler with the door and vehicle restraint.
Vehicle Restraints
Vehicle restraints come in many different applications – from a rotating hook or vertical barrier on the loading dock façade to ground mounted wheel-based restraints or wheel chocks. No matter the vehicle restraint type, the main purpose is to help keep trailers secure to the loading dock for safe loading and unloading.
Rotating Hook Restraints are widely considered the industry standard. The most advanced solutions can handle a wide range of trailer heights and can restrain obstructed rear-impact guards (RIGs), the metal bar across the bottom back of the trailer that the hook rotates up and engages with. The housing is mounted to the outside of the loading dock wall between the ground and the bottom of the dock opening. It requires electrical to communicate with dock controls inside the loading dock as well as traffic-style lights outside the building.
Vertical Barrier Restraints work similarly to rotating hook restraints as they engage with the RIG, but primarily applying upward pressure. Vertical barrier restraints come in three different styles for architects and general contractors to consider – ground-stored from a unit that is affixed between the wall and ground; wall mounted, which is self-explanatory; and an under-leveler version that features a recessed design that stores beneath the dock leveler pit. Push-button varieties require electricity to function.
Stabilizing Vehicle Restraints offer increased stability to forklift operators during loading and unloading of trailers. Hydraulic cylinders are mounted to the ground and the device also is connected with the wall, engaging the trailer RIG with a rotating hook. If your facility receives many trailers with air ride suspension or supports AGVs, a stabilizing vehicle restraint is the best option for your application.
Wheel-based Restraints offer solutions for trailers that don’t typically have RIGs, such as liquid tankers, as well as trailers with liftgates. These restraints use a bar that engages between two rear wheels to help secure the trailer in place. Some models are operated manually and only need to be mounted to the ground, while automatically engaging restraints need electrical connections.
Loading Dock Enclosures
Facilities control environmental factors at the loading dock using loading dock seals and enclosures. While the gateway is essential for products to flow in and out, it’s also an unfortunately easy spot for outdoor contaminants and pests to enter facilities.
Loading dock seals offer the most efficient seal. However, these foam pad seals can be damaged more easily than other options. Additionally, they often balloon out into the back of the trailer, reducing access to the trailer.
Loading dock shelters that are designed properly can offer an excellent seal to keep conditioned air inside a facility while minimizing outdoor contamination. They also offer full access to the back of the trailer, which increases productivity of material handling workers. These types of enclosures are typically the best choice for facilities.
Other considerations for loading dock enclosures are overhead rain diversion products and corner seals in the lower corners of the dock opening, which can be difficult to block.
Overhead Doors
Most loading dock openings are approximately 9 feet wide by 10 feet tall and use an overhead door to cover it when active loading or unloading isn’t happening. However, larger or smaller dock doors may be required depending on the application. Most doors are operated by push-button controls and need electrical hookups, although manually operated dock doors are still available.
Other options to be considered for loading dock door specifications include windows, ventilation options, and “impactability.” Impactability is the ability of the door to withstand a hit from forklifts, pallets, or other equipment, without needing much repair.
Different Loading Docks Require Different Equipment
A loading dock at a big box distribution center is going to look different than a dock at a food and beverage facility. Understanding the specific application of the loading dock, the types of trailers that frequent the dock, and how products will be loaded and unloaded in the material transfer zone will ultimately determine what pieces of loading dock equipment should be specified.
Architects or general contractors who need a second opinion can work with the experts at Rite-Hite for a loading dock tutorial or a free assessment for specific projects.
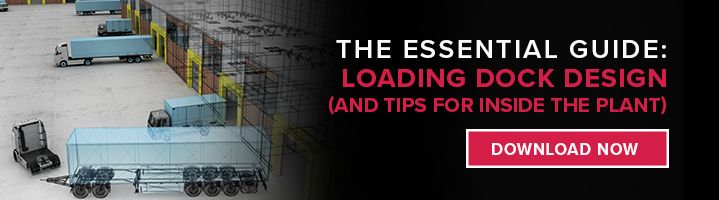
Contact Us Find a Rep