6 Universal Industrial Manufacturing Safety Regulations
The U.S. Occupational Safety and Health Administration (OSHA) is one of the most significant regulatory bodies of its kind in the world, as a considerable number of its codes apply to broad areas of general industry. Whether a facility is developing cars or shoes, it’s essential manufacturing facilities adhere to all the safety regulations that apply. Here are six that all facilities should know and follow.
- Home
- News
- 6 Universal Industrial Manufacturing Safety Regulations
6 Universal Industrial Manufacturing Safety Regulations
The U.S. Occupational Safety and Health Administration (OSHA) is one of the most significant regulatory bodies of its kind in the world, as a considerable number of its codes apply to broad areas of general industry. Whether a facility is developing cars or shoes, it’s essential manufacturing facilities adhere to all the safety regulations that apply. Here are six that all facilities should know and follow:
1. OSHA 29 CFR 1910.176: Materials Handling (U.S.)
1910.176(a)
Where mechanical handling equipment is used, sufficient safe clearances shall be allowed for aisles, at loading docks, through doorways and wherever turns or passage must be made.
Removing clutter is a first step toward keeping employees safe from congestion, blind spots and unprotected fall hazards. However, an even higher degree of safety can be attained with the right combination of equipment.
For example, inside the loading dock area, red/green dock lights indicate that a trailer is locked and safe to enter (or, to a truck driver, unlocked and safe to pull away). However, stacked pallets can obscure a lift driver’s view of them on the control panel.
To solve that issue, an enhancement was developed, with highly visible LED lights placed in the upper corners of dock doors. As a result, forklift operators can see the red/green signal even if the control box lights are obstructed. Additionally, red/green lights can also be placed on the leveler, thereby letting forklift operators within the trailer know that it is still safely secured to the loading dock.
2. OSHA 29 CFR 1910.212(a)(3)(ii): General Requirements for All Machines (U.S.)
Implemented by OSHA, this “umbrella” standard applies very broadly. It dictates that every machine should be guarded if its operation exposes employees to injury. Guarding devices should be designed and constructed in a manner that prevents operators from having any part of their bodies in danger zones throughout the operating cycle.
At its most basic, this regulation mandates machine guarding devices like automated barrier doors or presence sensors around machine process cells. More recently however, safety minded facilities have been expanding the definition of operations that “expose employees to injury” to include automated stretch wrap machines.
3. OSHA 29 CFR 1910.28: Walking-Working Surfaces (U.S.)
This code ensures that the protection of workers – from falling off the edge of an open dock position, as well as into recessed pit areas – should be a priority for facility and safety managers. Fixed barriers aren’t practical in loading dock areas because workers need to move across the leveler and into a truck’s trailer to load and unload products. Retractable barriers, which may help prevent forklifts from carrying heavy loads, are essential to use at the end of loading dock positions, especially when doors are open and trailers aren’t secured.
4. OSHA 29 CFR 1910.1000: Air Contaminants (U.S.)
Indoor air quality (IAQ) is critical to worker health. Paragraphs A through D of this regulation are primarily focused on limiting exposure for workers based in plants where air quality risk is present. Meanwhile, paragraph E illustrates that IAQ can be controlled with approved protective equipment and other best practices.
Some of these practices include implementing high-volume, low-speed (HVLS) fans, industrial fabric curtain walls and forced air distribution methods. HVLS fans can reduce exposure to harmful air contaminants by mixing (destratifying) the air, while fabric curtain walls can help separate areas where air contaminants are present from those where they are not. Fabric ductwork systems can also play a significant role. Some are made of fabric that diffuses across the length of the duct, which provides an even flow of clean air into a workspace – unlike metal ducts that only have diffusers in certain points.
5. OSHA 29 CFR 1910.900: Ergonomics (U.S.)
This newer standard contains stringent requirements for most non-construction employers to identify and abate musculoskeletal disorders. The standard identifies five such risk factors, which are defined in terms of “action triggers,” based on the duration of exposure to specified actions or conditions. The risk factors called out in this regulation are:
- Repetition
- Force
- Awkward postures
- Contact stress
- Vibration
While written safety protocols are a great starting point, leading facilities will go a step further toward preventing musculoskeletal disorders by installing equipment that reduces heavy repetition, force, awkward postures, contact stress and vibration. For example, instead of workers having to position heavy dockplates or dockboards that provide a bumpy ride for forklifts, facility managers should consider hydraulic levelers. These levelers typically provide smoother transitions from the facility floor into the trailer than dockplates or manually operated pull chain levelers. Leading models are specifically designed to reduce this bumpy “dock shock” sensation at both the rear and tip of the trailer.
6. OSHA 29 CFR 1910.95: Occupational Noise Exposure (U.S.)
According to CFR 1910:95, if employees are exposed to sound levels that exceed 85 decibels on an 8-hour time-weighted average (TWA), measured on the A scale (slow response), their employers are responsible for developing, executing and monitoring a hearing conservation program. This program, in particular, encompasses PPE, along with hours of tests.
To avoid the hours of work that are necessary to establish a hearing conservation program, along with thousands of dollars of unproductive testing time, facility managers can instead invest in flexible sound attenuation curtain walls.
Specific models of industrial curtain walls – consisting of two layers of woven, coated fabric surrounding insulating materials like fiber batting – can actually provide noise reduction of up to 25 dBs. And because they aren’t permanent walls, curtain walls can be installed easily and quickly, then reconfigured if the needs of a facility changes.
Safety is always a priority
Protecting workers goes a long way in industrial manufacturing. Be sure to follow catch-all safety regulations like the OSHA regulations mentioned above, as well as any that pertain specifically in your industry.
This blog was developed from the Essential Guide: Safety Regulations. For additional information on these topics and a full list of sources, click here.
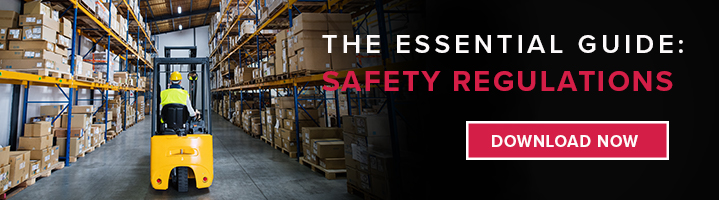
improving industrial safety, security and productivity worldwide
THROUGH QUALITY AND INNOVATION