- Home
- News
- 4 Warehouse and Distribution Center Design Trends
4 Warehouse and Distribution Center Design Trends
There’s no doubt about it, today’s warehouses are bigger and taller than they were two decades ago. According to research done by real estate and logistics services firm CBRE Inc., the average size of a warehouse doubled between 2002 and 2017. The average facility size increased 143%, up to 184,693 square feet, and the average warehouse height rose by nearly 4 feet up to a little more than 32 feet tall.
The growing warehouse is the first of four major design trends that are poised to take hold this decade. A variety of other paradigm shifts are taking place across the supply chain landscape, as well, including:
- the renovation and repurposing of buildings originally built for retail or other purposes
- incorporation of Internet of Things (IoT) into facility design
- and the use of automation across almost all phases of operations
1. Bigger Warehouses
The largest warehouse expansions (and new construction projects) have been on the fringe of huge metropolitan areas, which have big populations coveted by online sellers, as well as the abundant land that developers need. Examples include Southern California’s “Inland Empire” (just east of Los Angeles), the greater Atlanta area, and greater Cincinnati.
E-commerce growth over the past 5 years or so has created the need for massive warehouses with high ceilings to store extensive and fast-moving inventories. Because e-commerce demand is only expected to increase, this means that markets without enough modern logistics facilities will see continued construction as they play catch-up.
While industry insiders are split as to whether the trend to build vertical is more pronounced than the trend to build horizontal, there are compelling reasons for both approaches. Much has been made of the trend toward smaller facilities in urban areas, but an equivalent trend has taken root in farther-suburban and rural areas: mega-warehouses.
Overall, the general theme seems to be higher, wider, and more abundant. There are also parallel trends of warehouses “building up” (incorporating higher ceilings on a small or existing footprint) versus “building out” (incorporating broader horizontal footprints).
2. Renovation and Repurposing Buildings
There is a strong demand for buildings with larger footprints, high ceilings and close proximity to major population centers; however, land availability and cost are two major concerns. Not surprisingly, an anticipated trend is the conversion of old retail facilities and shopping centers into warehouses and distribution centers because the land, structure and resources already exist.
Recent research by CBRE (as reported in Material Handling and Logistics’ February 2019 issue) confirmed this trend is already taken place. Since 2016, 24 projects across the country that had 7.9 million square feet of retail space were converted into 10.9 million square feet of industrial space — through either converting the retail building or demolishing and replacing it.
3. Incorporating Smart Manufacturing into Facility Design
In any foreseeable future, the roles of IoT and artificial intelligence (AI) are expected to continue growing. Not only do they help distribution centers better predict demand and reduce inventory costs, they enhance safety and productivity and can decrease energy costs.
The information provided by IoT can help managers uncover potential challenges and proactively identify solutions, driving behavioral and process changes. IoT is particularly adept at monitoring and communication, which can have a significant impact on organizational safety (as well as boosting efficiency and productivity). In fact, 93% of manufacturers agree that IoT benefits exceed risks, as reported in an Industry Week study.
At loading docks with data-capturing smart controls, equipment enhanced with IoT capabilities can give facilities a more advanced look at what’s happening during logistics operations. For example:
- Vehicle restraints: By connecting with IoT loading dock management software, these pieces of equipment can share information on which loading docks are available for loading/unloading and when a vehicle restraint goes into fault, so facility managers can immediately react to a potentially unsafe situation.
- Audio and visual light communications systems: These motion-sensor activated systems indicate when there is a restraint fault, if someone enters an unsecure trailer or tries to disengage a trailer with activity inside the trailer.
- The system also tracks when doors go up, levelers down, etc. as well as how long and how many cycles they’ve recorded.
4. Use of Automation
Automation has become a fact of life for manufacturers across the world. According to Production Machining magazine, more than half (56%) of global companies currently use some type of automation – and that number is quickly rising. While 10% of today’s manufacturing functions are automated, Boston Consulting Group (BCG) predicts this number will rise to 25% as robotic vision sensors and gripping systems improve. BCG also estimates that roughly 1.2 million industrial robots are expected to be deployed by the year 2025.
For most manufacturers, this is a good thing, given the shortage of available workers with warehouse experience. However, many feel that automation is really shifting workers to other jobs, rather than replacing them.
The need for safety barriers is going to increase due to automation, particularly autonomous vehicles or automated storage and retrieval systems, as well as the need for warehouse and distribution center operators to meet OSHA regulations, and promote its own safety culture.
That means there will continue to be a need for safety products, such as mezzanine and rack safety gates, floor-level safety barriers, motion sensors and LED safety systems, and vehicle restraints at loading docks.
Getting Up-to-Speed on Warehouse Trends
It’s important for organizations to understand these trends to better prepare their warehouse or distribution center for the future. It’s up to the facility manager to make sure that their facility has the right equipment and the right staff to help provide a safe and productive workplace that can meet the ever-increasing demands of consumers. To learn more about design trends for warehouses and distribution centers, download our Essential Guide: Warehouses and Distribution Centers.
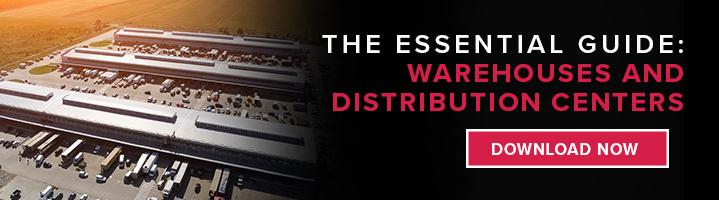
Contact Us